Anúncios
In the world of industrial work, good plant maintenance is a must. Using strong maintenance plans is key to keep equipment last longer and work better. By being proactive, companies can cut downtime and boost their work output.
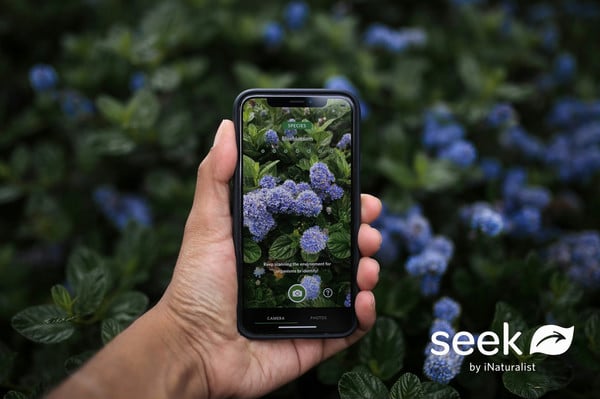
Seek App
This article will share important tips, tools, and ways to better plant maintenance. With a smart maintenance plan, companies can save a lot of money. They also can make their machines last longer.
Anúncios
Understanding Maintenance Planning
Maintenance planning is key for smooth running in any place. By planning well, tools can last longer and work better. It’s important for places to focus on their maintenance plans. This helps avoid sudden breakdowns, keeps things reliable, and controls costs.
Importance of a Maintenance Plan
For any organization, having a strong maintenance plan is a must. It helps prevent equipment from failing unexpectedly. When you have a good maintenance strategy, you’re on top of inspections and fixes. This stops problems from getting bigger, keeping work flowing and equipment dependable.
Anúncios
Components of Effective Maintenance Planning
An effective maintenance plan has important parts:
- Regular checks to see how equipment is doing
- Quick fixes for any problems found
- Smart use of resources for the best performance
- Matching maintenance goals with the organization’s overall aims
Having clear goals for maintenance and looking at how well things are going are key. These steps keep tools working at their best. This ensures work keeps going smoothly and equipment stays reliable.
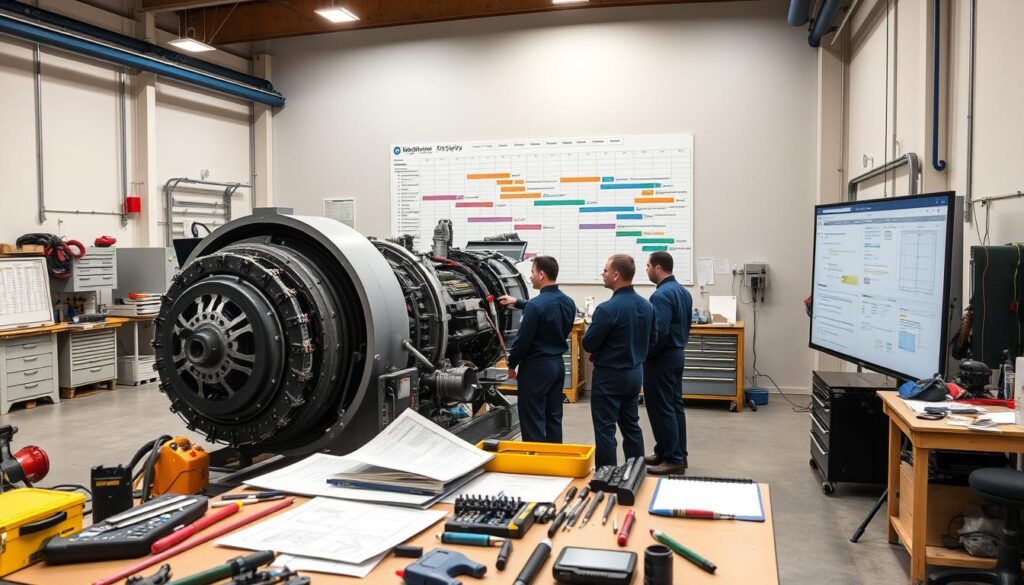
Benefits of Preventive Maintenance
Effective preventive maintenance has many benefits for facilities. The biggest benefits include less downtime and longer equipment life. By knowing these advantages, groups can create a better plan for their maintenance work.
Minimizing Downtime
Preventing downtime is a major perk of preventive maintenance. By doing regular checks and upkeep, sudden machine failures are greatly lowered. Dealing with issues early stops them from getting bigger, which can save money and trouble.
Increased Equipment Lifespan
Boosting how long equipment lasts is also key. Doing simple things like oiling and proper servicing helps machines work better. This care cuts down on expensive fixes and means companies don’t have to buy new equipment too soon, saving money in the long run.
Differentiating Maintenance Strategies
It’s key to know the different maintenance strategies for better plant operations. Different methods can greatly affect efficiency, costs, and how long equipment lasts. By comparing maintenance strategies, we see the pros and cons of each. This makes it easier to pick the best strategy for a business’s needs.
Reactive vs. Preventive Maintenance
Reactive maintenance means fixing things only after they break. This might seem like a good way to save money, especially for machines that aren’t crucial. But, it often leads to unexpected shutdowns and more problems. On the other hand, preventive maintenance involves regular checks and fixing things before they break. This approach keeps machines running well, boosting productivity.
Predictive and Condition-Based Maintenance
Predictive maintenance uses technology to guess when equipment will fail. It uses data and sensors to plan maintenance before problems happen. Condition-based maintenance watches the actual condition of machines, fixing them based on signs of wear. This smart way of doing maintenance improves efficiency and avoids unnecessary work.
Setting Maintenance Goals
It’s vital to set clear maintenance goals for a strong strategy. By using the SMART criteria, goals become focused and actionable. This approach aligns them with the wider aims of the business. SMART goals are Specific, Measurable, Achievable, Relevant, and Time-bound. This helps businesses improve their operations.
SMART Goals Framework
The SMART framework is a key tool for making maintenance goals. For example, a goal might be to cut equipment downtime by 10% in four months. This would be through special maintenance efforts and team training. Providing such specifics helps clearly outline the goals and how to measure success.
Aligning Maintenance Goals with Business Objectives
Maintenance goals should line up with business aims to be most effective. They need to focus on boosting productivity, increasing safety, and following regulations. Keeping maintenance teams and leadership in constant talk helps goals stay in tune with business changes.
Assessing Your Current Maintenance Operations
To make your maintenance better, it’s key to check what you’re doing now. Doing a deep-dive audit and looking at maintenance data helps a lot. It shows what’s working and what’s not, so you can fix problems before they get bigger.
Conducting a Maintenance Audit
Checking on how your assets are doing is key with a maintenance audit. This includes:
- Listing all your equipment to see how old it is and its condition
- Looking at past fixes to see if there’s a common issue
- Seeing how well your current fixing methods are working
By really digging into your maintenance work, you find out what needs more care. You also figure out how to make things run smoother.
Analyzing Maintenance Data
Looking at maintenance data is super important to spot trends that might need a change in how you do things. By checking:
- How much spending on fixes
- How often equipment breaks down
Organizations spot patterns that help make smart choices. Regularly checking this helps move from fixing after a break to preventing issues. This makes everything work better.
Developing a Maintenance Strategy
Making a maintenance strategy means knowing what your business needs. You need to figure out the best ways to keep your equipment running. This includes using preventive, predictive, and reactive maintenance techniques. These methods help make a plan that suits your machines and your business goals.
Good maintenance planning means checking equipment regularly and fixing things on time. By putting in place a set process for these tasks, companies can work more reliably and keep costs down. It’s important to make sure there are enough resources for all maintenance work.
When creating a maintenance strategy, think about:
- Assessing equipment criticality and failure risks
- Creating routines for maintenance schedules
- Utilizing data and analytics to inform decision-making
This careful planning can greatly reduce equipment downtime and lower maintenance costs. It leads to better productivity. A well-thought-out maintenance strategy helps with daily tasks and keeps equipment running longer.
Plant Maintenance Best Practices
It’s key to apply best practices in plant maintenance for better work and longer equipment life. Regular check-ups help spot issues early, avoiding big problems later. These checks keep machines working well, make the workplace safer, and help things run smoothly.
Implementation of Regular Inspections
Checking equipment often is vital for keeping things running right. It lets teams fix small problems before they get big, saving money and avoiding unexpected work stops. A set schedule for inspections ensures all important parts get the care they need.
Proper Resource Allocation
Managing resources well is crucial for maintenance work. It means using tools, people, and time wisely so tasks get done fast. Good management prevents shortages that could cause delays. Investing in training and quality tools pays off by boosting efficiency and making things last longer.
Creating a Maintenance Schedule
Creating a good maintenance schedule is key to keeping things running smoothly. It helps make sure tasks are done on time and cuts the chance of equipment breaking down. By putting the most important maintenance tasks first, businesses can use their resources better and keep downtime low.
Prioritizing Maintenance Activities
To schedule maintenance well, it’s important to figure out which tasks are most urgent and crucial for the business. This way, machines that are very important and at high risk of breaking down are taken care of first. Looking at things like how often machines are used and how reliable they are helps decide what to fix first. This careful planning reduces risks and boosts work efficiency.
Frequency of Maintenance Tasks
How often maintenance tasks need to happen depends on the type of machinery and how it’s used. Starting with what the machine’s maker suggests is a good base, but sometimes changes are needed. These changes might come from what has been learned over time or past performance. Knowing how often to do maintenance tasks makes for a stronger schedule and can make machines last longer.
Implementing a Preventive Maintenance Program
A preventive maintenance program needs careful planning. It makes sure machines and equipment are always in good shape. Starting with a clear plan means checking and fixing things regularly. This reduces sudden breakdowns and makes things last longer.
Checklists help keep routine maintenance on track. They include all necessary steps like oiling, adjusting, and checking parts. By keeping records of maintenance tasks, companies ensure nothing is missed. This helps in keeping track of the maintenance work.
Training employees on maintenance is crucial. They need to know what to do and why it’s important. Learning the right way to do things helps avoid problems and saves time. Keeping detailed records of maintenance work helps improve the process over time.
Utilizing Maintenance Software
Advanced maintenance software solutions are key to effective maintenance strategies. Tools like Computerized Maintenance Management Systems (CMMS) are changing the game. They make maintenance tasks easier and help see the whole picture of how assets are doing.
Benefits of Computerized Maintenance Management Systems (CMMS)
Using a CMMS adds a lot of value to maintenance work. Here are the main perks:
- Enhanced asset tracking and visibility
- Streamlined scheduling for maintenance tasks
- Improved documentation management
- Increased accountability among team members
- Easier data analysis for strategic insights
This approach makes using resources more efficient. It lets organizations tackle maintenance needs head-on.
Integration with Other Business Systems
For better efficiency, integrating business systems is key. Linking maintenance software with inventory and accounting boosts data sharing. This integration offers several advantages:
- Reduced administrative overhead
- Consolidated access to vital information
- Improved strategic planning capabilities
Maintenance software improves maintenance tasks and helps meet bigger company goals. It sets the stage for ongoing top performance.
Monitoring and Improving Maintenance Processes
Optimizing equipment efficiency and cutting costs need effective monitoring of maintenance. Setting up Key Performance Indicators (KPIs) for maintenance helps teams evaluate their work. These indicators track important stats like mean time between failures and how well equipment works. By focusing on these KPIs, groups can find and fix weak spots, improving how things run.
Establishing Key Performance Indicators (KPIs)
Measuring success in maintenance uses vital tools called KPIs. These are key metrics:
- Mean time to repair (MTTR)
- Equipment downtime
- Scheduled maintenance compliance
Looking at these indicators regularly helps make processes better. This ensures that maintenance plans support the business’s main goals.
Continuous Improvement Strategies
Improving maintenance constantly is an active, ongoing task. The backbone of this approach is getting regular feedback from maintenance teams. Adding data analysis and team insights lets companies make real plans for betterment. Using root cause analysis and focusing on preventive maintenance trends are key. They help create a flexible maintenance environment.
Environmental and Safety Considerations in Maintenance
Maintaining the environment and keeping everyone safe is key to good maintenance work. It is important to keep up with laws that help protect our health and the world around us. Making sure safety is part of daily tasks reduces risks and helps everyone focus on being safe.
To do this well, companies need to:
- Conducting regular safety audits to identify potential risks and ensure adherence to compliance considerations.
- Provide training often to remind employees about safe and eco-friendly ways to work.
- Have a good plan for handling dangerous materials, including how to get rid of them safely.
By working these steps into their maintenance plans, companies do more than just follow rules. They also make their operations run better and safer for everyone.
Conclusion
Maintaining plants well is key to achieving the best operational efficiency. Effective maintenance, especially preventive, makes equipment last longer and work better. It helps businesses cut down on costs and makes the workplace safer.
Also, using modern tech like computerized systems makes maintenance smoother. It helps managers make better choices. Aligning maintenance goals with the company’s overall aims keeps businesses competitive in the fast-changing market.
To conclude, it’s important to always look for ways to improve maintenance. Being proactive in maintenance practices strengthens business operations. It helps companies stay strong amid industry changes.